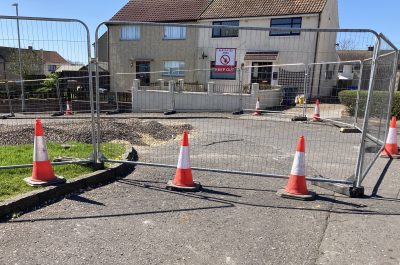
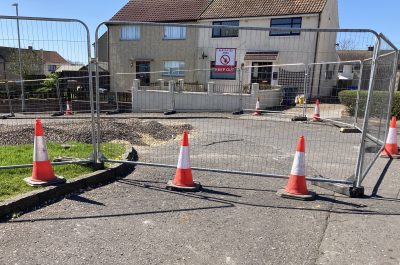
The purpose of the works was to investigate and consolidate the mine shaft in order to mitigate the risk of further collapse and to ensure ground stability. The works compromised four distinct phases, with design review periods between.
The ground investigation works comprised 4 No. cable exploratory cable percussive boreholes with rotary core follow on (69.25 linear drilled metres). These holes were carried out to determine subsurface ground and groundwater conditions adjacent to the collapse.
The second phase of works comprised 4 No. inclined rotary probe holes, sunk from outside the exclusion zone towards the collapse, to locate the position of the shaft, followed by the installation of 20m safety platform to carry out a further 15 No. probe holes within the collapse zone to confirm the exact location, dimensions and depth of the feature (631.50 linear drilled metres)
Phase three commenced with the installation of a larger 24m bailey bridge, installed via a crane lift, to allow consolidation works to take place over a wider area. The ground stabilisation works involved drilling a grid of rotary percussive treatment holes and the injection of a resin grout to render the feature stable. A total of 22 No. rotary percussive holes (478.0 linear drilled metres) were drilled and 4,267 litres of Master Roc MP355 Resin was injected into the workings.
Full depth treatment of the shaft was not considered suitable in this instance due to the presence of a high water table and mobile groundwater. The Designer required a ‘plug’ at the top of the shaft. MasterRoc MP355 Resin was selected as it can be injected discretely at a specific target depth to form a plug. Cementitious grout was not considered suitable as it would potentially to sink to the base of the shaft and displace large volumes of water in the vicinity of the adjacent residential properties.
The selected MP355 Resin product consists of two components, combined at point of use. The reaction produces an increase in product volume and results in an inert silicate resin. The period for the expansion and curing of the foam is between 90 -120 seconds, after which the foam is fully cured, combining the intermitted voids of the workings and the overburden to form a solid plug.
A permanent water monitoring installation was also installed to a depth of 74.00m within the centre of the feature to facilitate future monitoring.
During the fourth phase of works, 4 No. extensometers (100.5 linear drilled metres) were installed within and adjacent to the shaft to allow monitoring of any further ground movement in the future.
The phased approached undertaken by SEGL successfully achieved stabilisation of the abandoned mine entry, mitigating the risk of future ground collapse and risk to the local residents and the public.
The works were undertaken within the agreed timescales and effective communication between the client and SEGL throughout the project ensured that public safety was the priority whilst achieving the best value approach for successful consolidation.
The UK’s Water Industry National Environment Plan, or WINEP, currently requires water companies to undertake over 24,000 actions related to water quality and biodiversity, supported by investment totalling over £22 billion. As well as headline projects such as United Utilities’ HARP, Southern Water’s Havant Thicket reservoir, Water Companies across England are undertaking numerous smaller improvement […]
Read more ➜Soil Engineering providing expert drilling services to the University of Edinburgh’s Geobattery projectThe Coatbridge team of Soil Engineering’s Specialist Geoservices unit have secured a prestigious contract with the University of Edinburgh to provide the first borehole of their Geobattery Research Project. Drawing on specialist experience of drilling deep holes in coal bearing strata from within […]
Read more ➜Soil Engineering Geoservices have been shortlisted for a total of nine entries in the Ground Engineering Awards 2025! Collaboration, innovation, quality and determination providing a backbone to delivering some excellent projects across no fewer than seven categories in the 2025 Ground Engineering Awards. As a business we’ve achieved shortlist recognition for our overall delivery capability, […]
Read more ➜